Predictive Maintenance and Condition Monitoring
- Home
- / Case Studies
- /Predictive Maintenance and Condition Monitoring
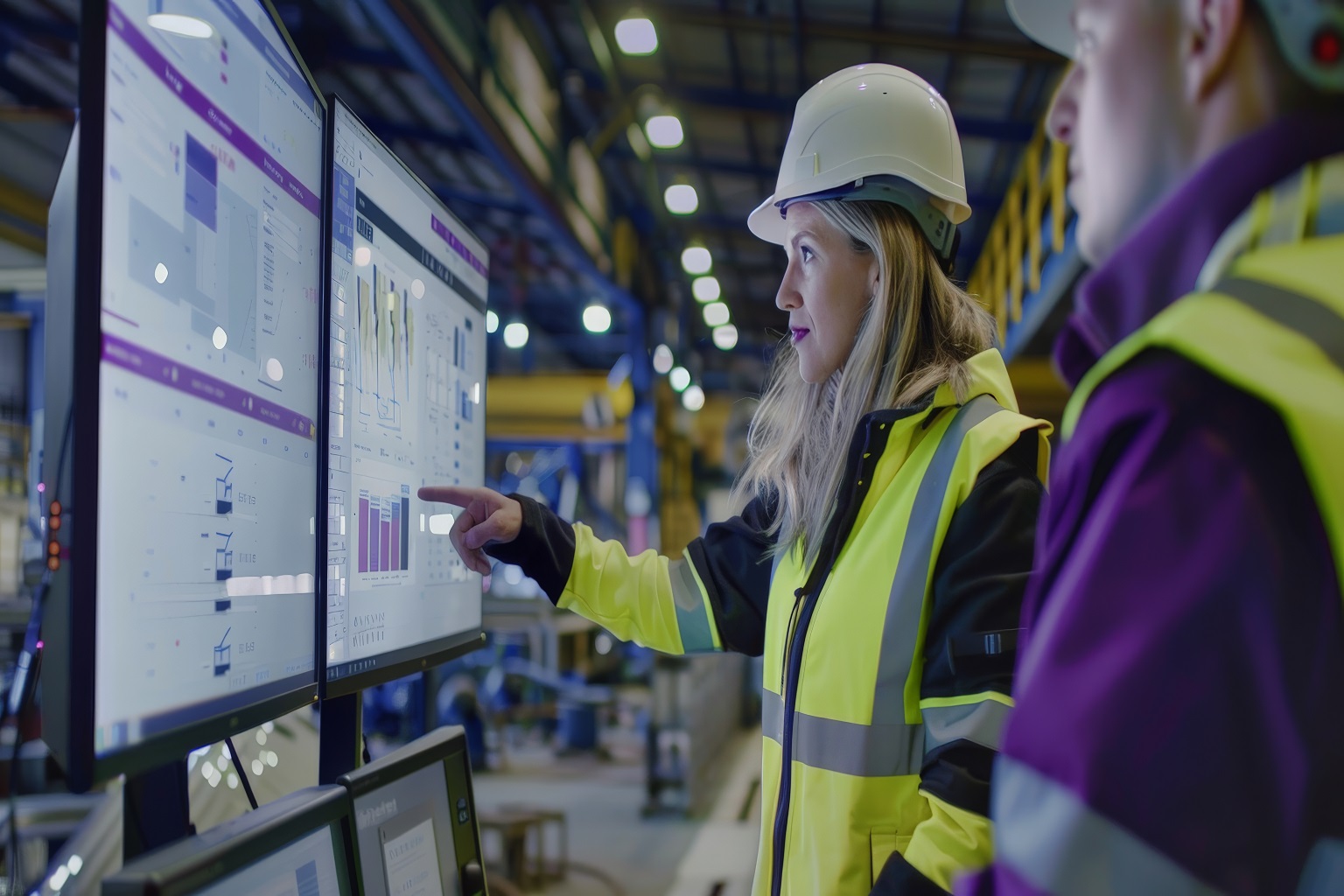
Client
The client is an industrial equipment manufacturer that operates critical machinery under an Annual Maintenance Contract (AMC). Their operations involve compressors, pumps, spindles, and motors, which require continuous monitoring to prevent failures and ensure operational efficiency. The client needed a remote monitoring solution to track equipment health, identify root causes of failures, and optimize maintenance schedules.
Challenges
- Lack of real-time equipment monitoring – Manual inspections were inefficient in detecting early-stage issues.
- Unexpected equipment failures – No predictive mechanism to detect potential breakdowns before they occur.
- High maintenance costs – Reactive maintenance led to costly repairs and extended downtimes.
- No centralized platform for monitoring and alerts – There was no automated system to analyze telemetry data, detect anomalies, and send maintenance alerts.
Our Solution: iThings-Powered Predictive Maintenance System
To overcome these challenges, iThings was implemented as an IoT-based predictive maintenance platform, enabling remote monitoring, real-time alerts, and AI-powered anomaly detection.
1. IoT-Based Condition Monitoring for Real-Time Equipment Health Tracking
iThings integrated smart sensors on industrial machinery to monitor vibration, temperature, and performance metrics. These sensors continuously collected real-time telemetry data and sent it to the iThings cloud for analysis.
2. AI-Driven Predictive Maintenance Models for Failure Prevention
iThings utilized Machine Learning algorithms to analyze historical performance data and detect anomalies. The platform predicted potential failures and estimated the remaining machine runtime, allowing for proactive maintenance scheduling.
3. Centralized Dashboard for Data Visualization and Alerts
iThings provided custom dashboards displaying equipment performance trends, predictive analytics, and root cause diagnostics. The system categorized equipment status into proactive, predictive, and reactive maintenance zones, helping maintenance teams prioritize actions.
4. Automated Alerts and Role-Based Access for Maintenance Teams
Field technicians and managers accessed iThings web and mobile applications, receiving real-time maintenance alerts, critical event notifications, and automated reports. The role-based access control ensured that the right personnel received relevant insights.
5. Seamless Integration with Factory Equipment and Cloud Storage
The system was integrated with edge gateways to process telemetry data locally before syncing with the iThings cloud. This ensured low-latency decision-making, allowing for immediate corrective actions when anomalies were detected.
Benefits of iThings Implementation
- Proactive issue detection – Prevent major failures by addressing early warning signs before escalation.
- Extended equipment lifespan – Optimized machine health with predictive analytics, reducing wear and tear.
- Improved motor and pump performance – Continuous monitoring ensured efficient operations without unexpected disruptions.
- Reduced maintenance costs – Predictive maintenance lowered repair expenses by eliminating unnecessary downtime.
- Energy savings – Optimized equipment efficiency, reducing overall energy consumption.
Tech Stack Used
- iThings IoT Platform
- Smart Sensors for Condition Monitoring
- Edge Gateways for Data Processing
- Machine Learning for Predictive Analytics
- Web and Mobile Application for Remote Access